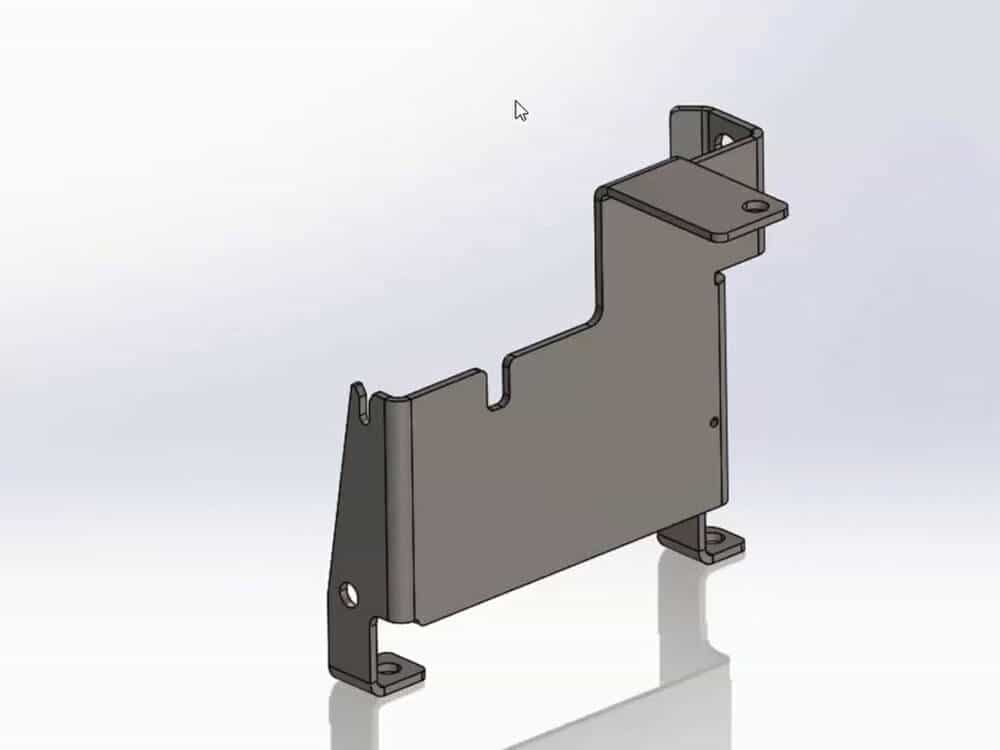
Design
DDI’s design engineers use the latest 3D Solidworks & AUTOCAD design software to produce conceptual designs and parts.
Our expert in-house design team works closely with customers from the beginning of each project to ensure that all assemblies are consistently successful at the prototyping stage.
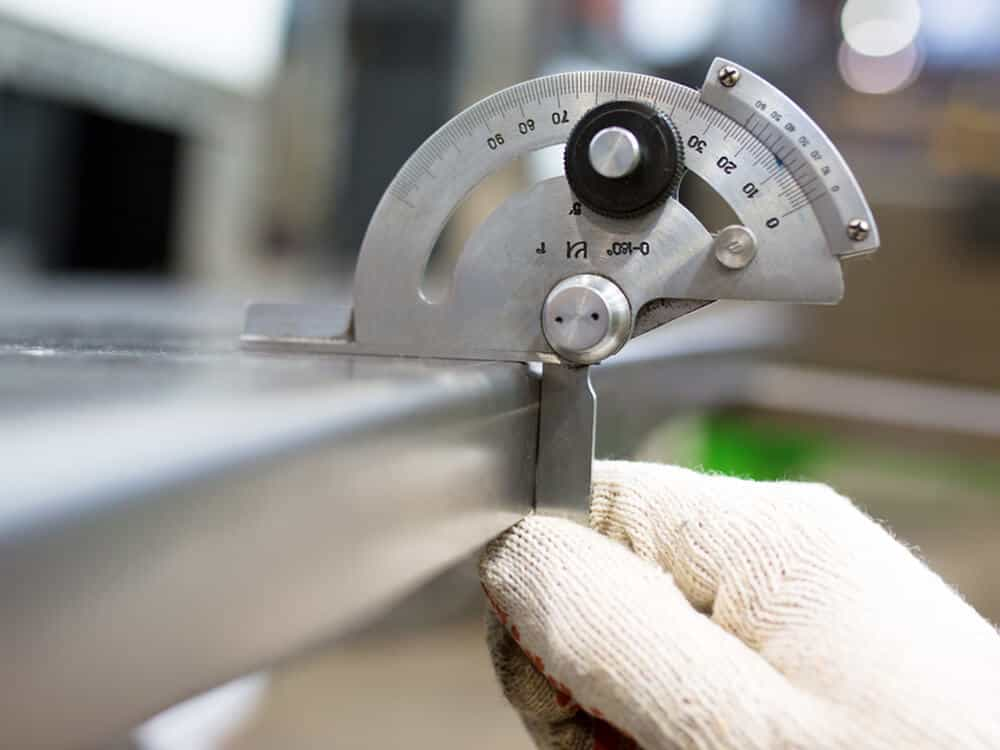
Rapid Prototyping
Our machining capabilities include Fiber Laser Cutting, Folding, 2D CNC Wire Bending, 2D Tube Bending, MIG and TIG Welding as well as Powder Coating to produce one-off metal prototypes in tube, wire, or sheet metal.
From receipt of production drawings DDI Engineering are able to complete a finished prototype in a very quick timeframe.
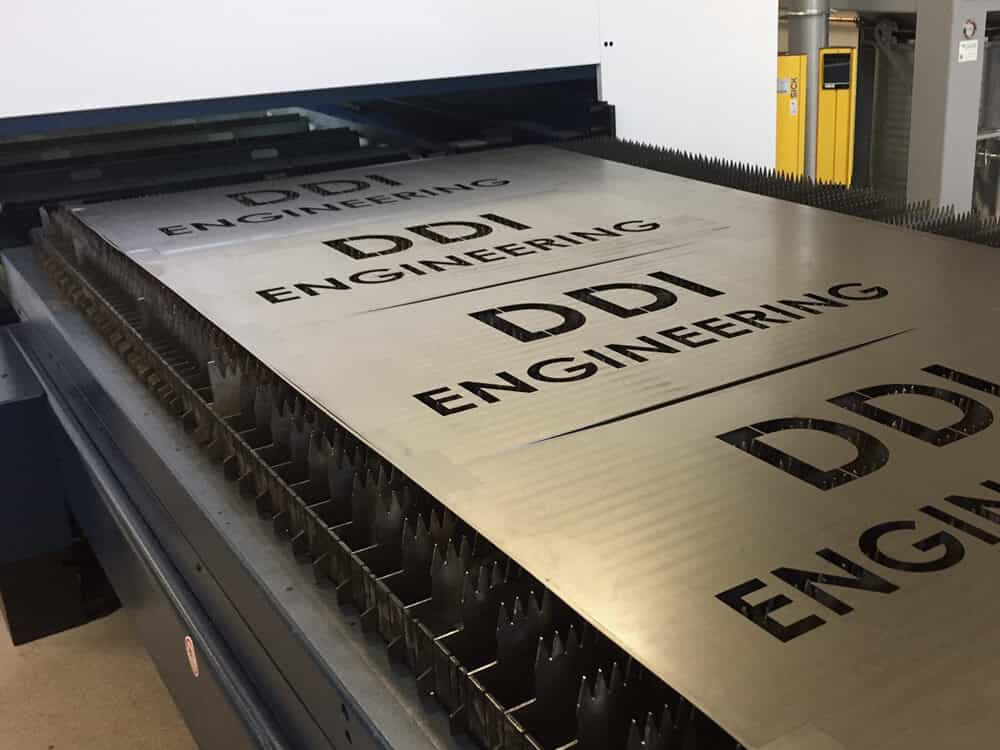
Fiber Laser Cutting
DDI have invested in a state-of-the-art Fiber Trumpf laser cutter to produce consistently accurate components across a wide range of materials and sheet thickness.
We can supply cut only parts or if required we can offer you additional services such as folding, welding and powder coating.
Laser Capabilities:
- Mild steel 20 mm
- Stainless steel 15 mm
- Aluminium 15 mm
- Copper 6 mm
- Brass 6 mm
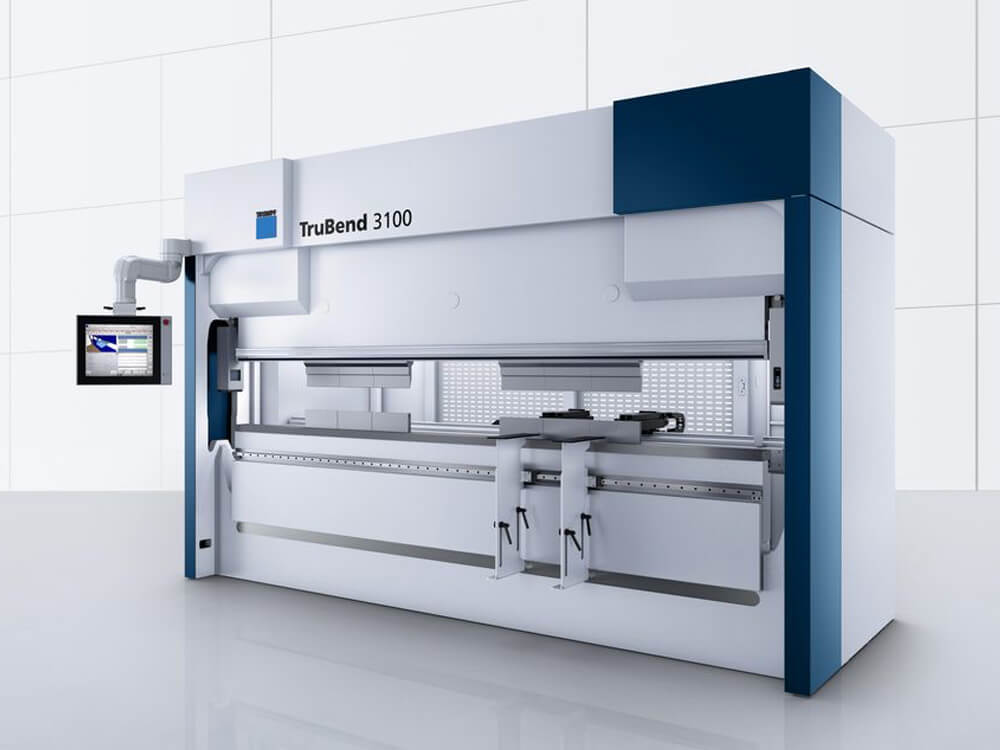
Folding
DDI Engineering have highly accurate press brakes ranging in size from 2 meter up to 3 meters. DDI Engineering also stock an extensive range of tooling to complement our other services, Fiber Laser Cutting, Folding, 2D CNC Wire Bending, 2D Tube Bending, MIG and TIG Welding as well as Powder Coating.
DD Engineering offers a first-class sheet metal rolling with the capability of rolling a width of up to 1200m. Roll-bending or curving, designates the manufacture of sheet-metal parts that are rolled or curved into cylindrical shapes or shapes that have a smooth radius associated with them.
As a result, we can roll mild steel, stainless steel and aluminium up to a thickness of 3mm.
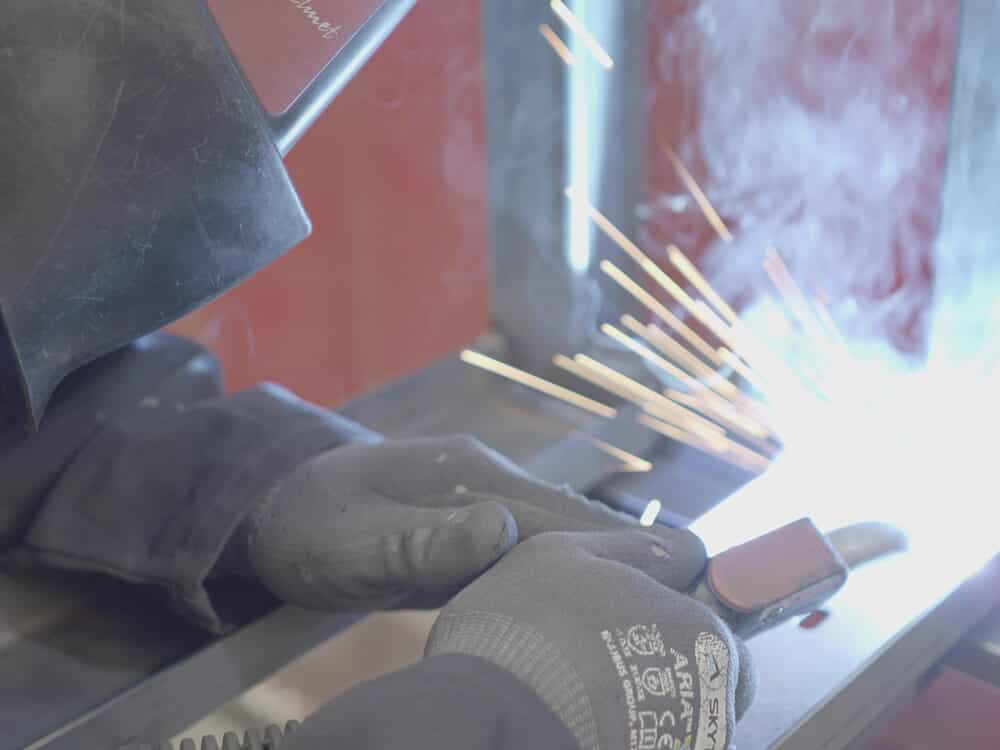
Fabrication & Welding
With over 30 years’ experience and 5 dedicated welding stations DDI can offer you all the welding and fabrication you require for your project.
From complicated one-offs to high volume production runs. In addition, DDI Engineering have 5 spot welding stations with the ability to spot weld sheet, mesh and wire.
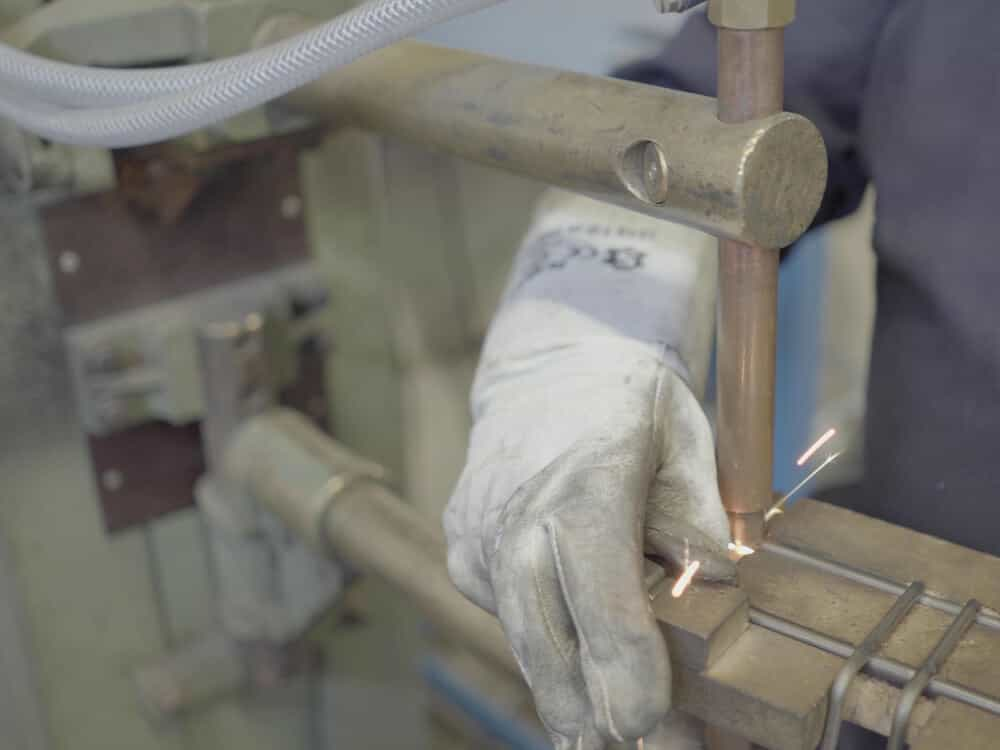
Spot Welding
Spot welding is one of the oldest welding processes. It is used in a wide range of industries. This is a type of resistance welding where the spot welds are made at regular intervals on overlapping sheets of metal or wire.
Spot welding is primarily used for joining parts that are normally up to 3 mm in thickness. We use the spot welding method to manufacture baskets, trollies, shelving and wire based product.
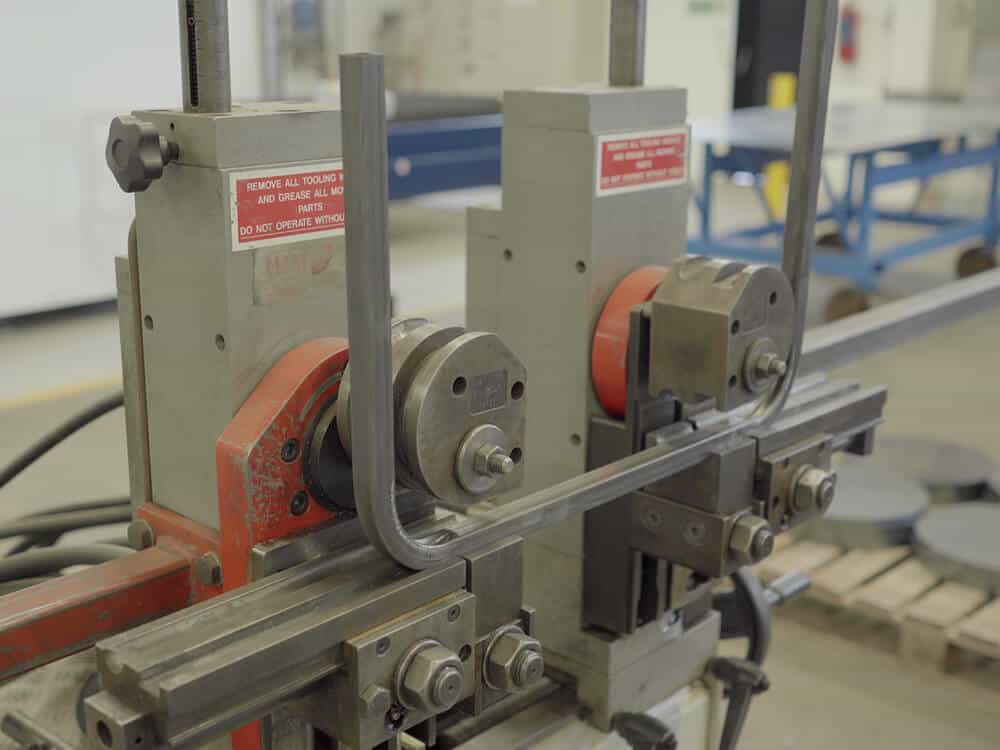
2D Tube Bending
When is come to round, square or rectangular tube DDI Engineering can offer you bending, cutting and rolling.
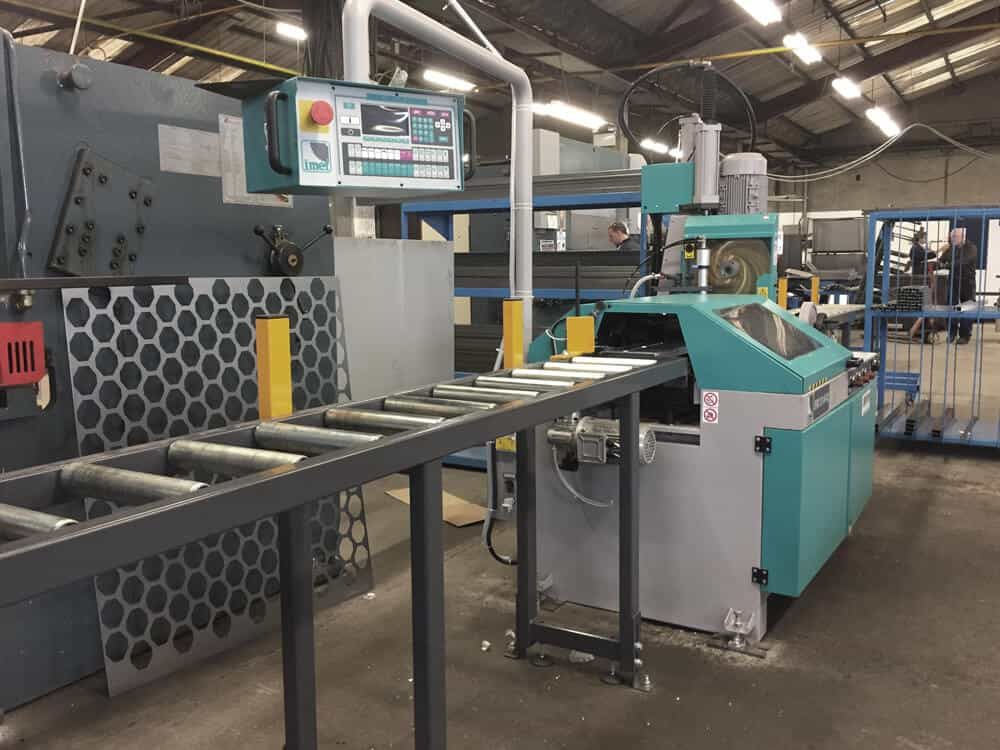
Tube Cutting
We are able to provide an in-house automatic saw cutting service enabling us to deliver a fast and accurate service to meet your requirements. We can cut square, rectangular, round & bar. Contact us for more info.
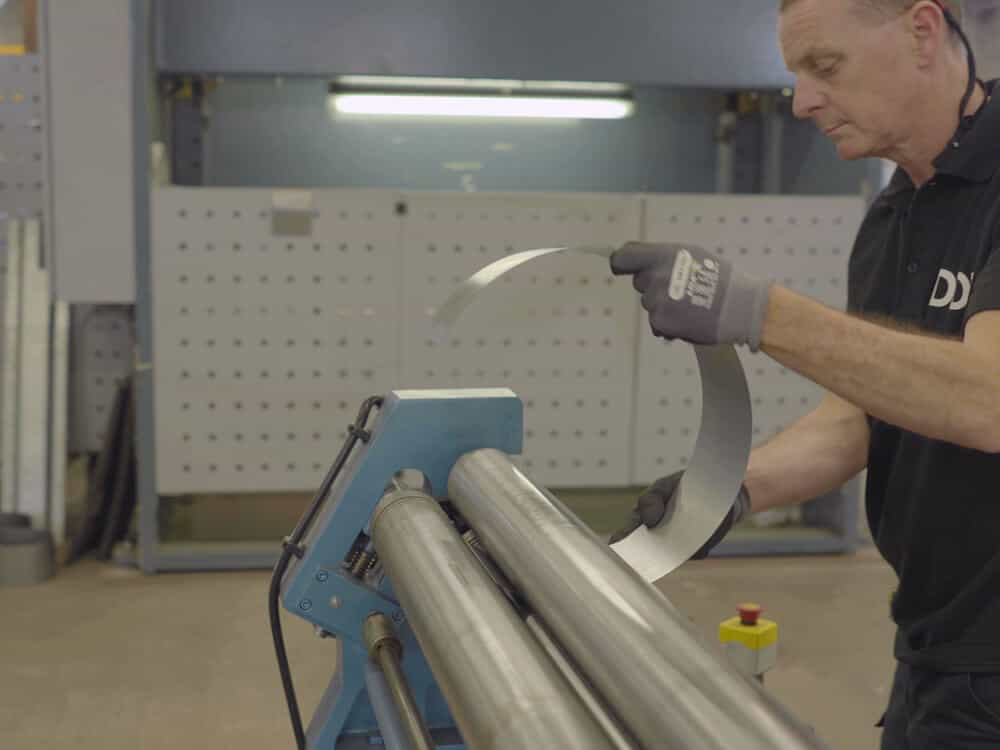
Sheet/Tube Rolling
DDI Engineering have the capabilities to roll steel and aluminum plate into full cylinders, cylinder segments, full cones, and cone segments. Sheet or plate rolled into tubular shapes can be used for conveyor pipes, downspouts, and numerous other applications.
We can produce both concentric and eccentric cones. We create cones from light gauge pipe for ventilation systems, via heavy plate rolling for metal duct work in steel mills, and everything in between. Plate rolling can also be used to form helical shapes for circular stair stringers.
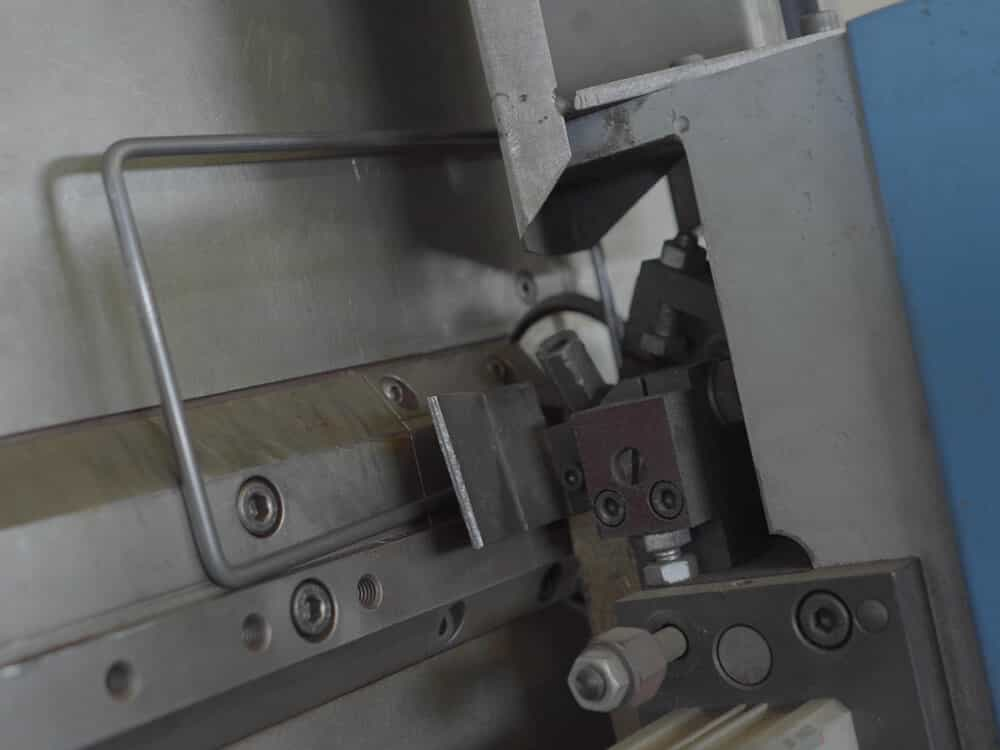
CNC 2D Wire Forming & Automatic Welding
Typical CNC wire formed products and components that we manufacture in high volumes include;
- Display racks
- D-arms
- Curved headers
- Chair frames
- Furniture frames
- Seat frames
- Support legs
- Tubular legs
- Tubular rings
- Spreader frames
- Storage units
- Work stands
- Guards
- Hand rails
DDI Engineering can process wire ranging from 2.00 mm up to 6.00mm.
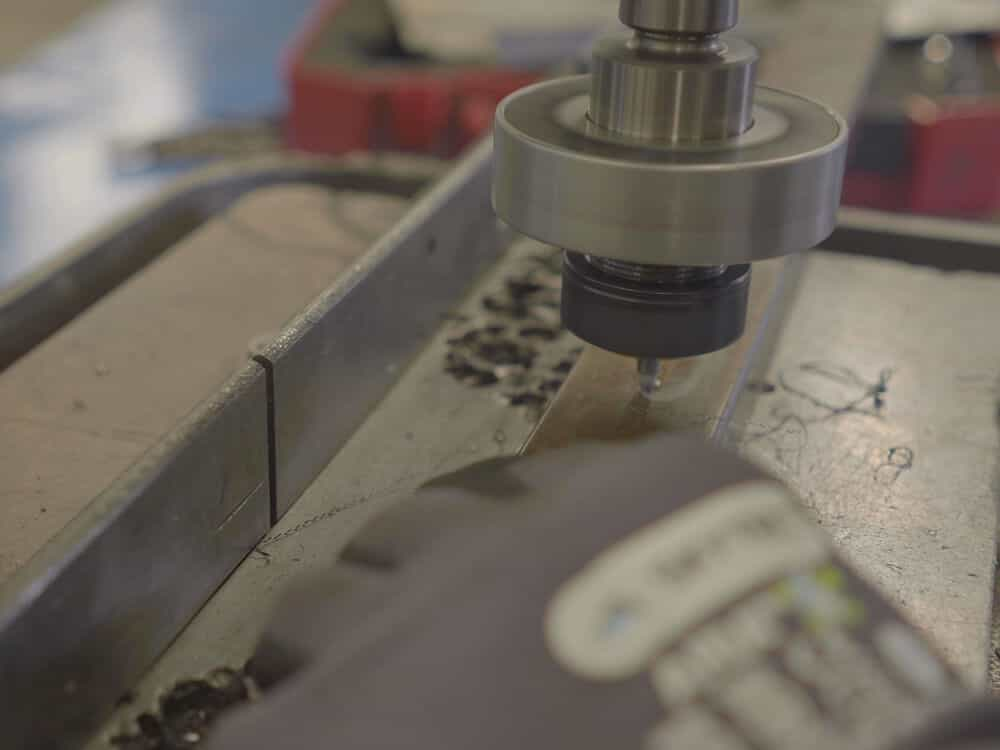
Flow Drilling and Tapping
Flow drilling is a thermal process for producing a bush from the parent metal. Many components require tapped holes for assembly.
This has always been a problem area when using tubular materials, due to wall thickness being so thin particularly where a thread pitch is greater than the wall thickness.
Using the flow drilling and tapping process, problems of tapped inserts spinning are avoided. With flow drilling and tapping, the bush formed will give three to four times the original material thickness in most cases.
Flow tapping removes none of the parent metal which enables us to tap into thin wall materials with a range of M3 – M12 threads.
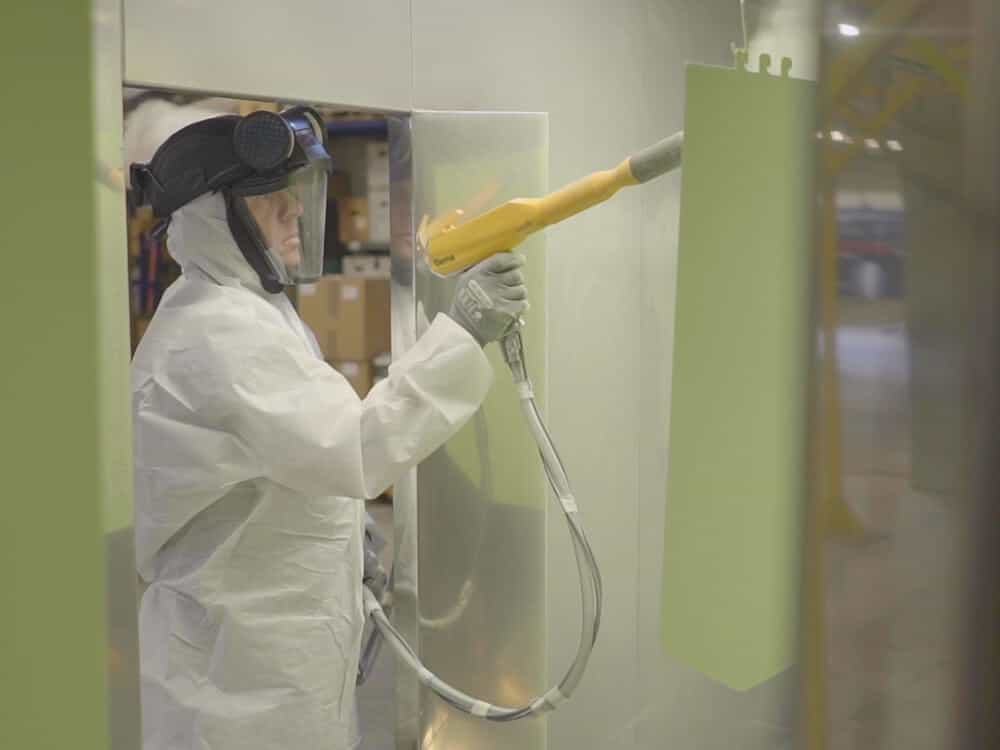
Powder Coating
DDI Engineering’s dedicated in-house powder coating plant ensures tight control on both efficiency and delivery and guarantees that quality remains our highest priority. If you require a reliable and high-quality powder coating service, then DDI can help. DDI have its own 3 phase powder coating plant in house.
Powder coating is a modern painting method that “bakes” paint onto a surface –The powder is made from resins and pigments; it is applied as a dry product through an electrostatic charged transfer process. Once the powder adheres to the component it cures in a temperature-controlled oven up to 220°C depending on the type coating.
Powder coating has proven to be extremely decorative and more resistant to chemicals, chipping, fading and wearing than other finishes. Powder coating is also extremely cost-effective when set against labour intensive traditional liquid coatings.
It is also virtually pollution-free, with very little wastage in the application process, containing no solvents and producing almost zero volatile organic compounds.